In engineering construction, rock bolts play a crucial role in ensuring the stability and safety of structures built on or within rock formations. These bolts are primarily used to reinforce and support rock masses, preventing potential collapses and ensuring the integrity of the overall structure. However, one significant challenge faced by rock bolts is the corrosive nature of the environment in which they are installed. Over time, corrosion can weaken the bolts, compromising their effectiveness and jeopardizing the safety of the entire construction. This is where the double corrosion protection self-drilling rock bolt comes into play, offering a superior solution compared to ordinary self-drilling rock bolts.
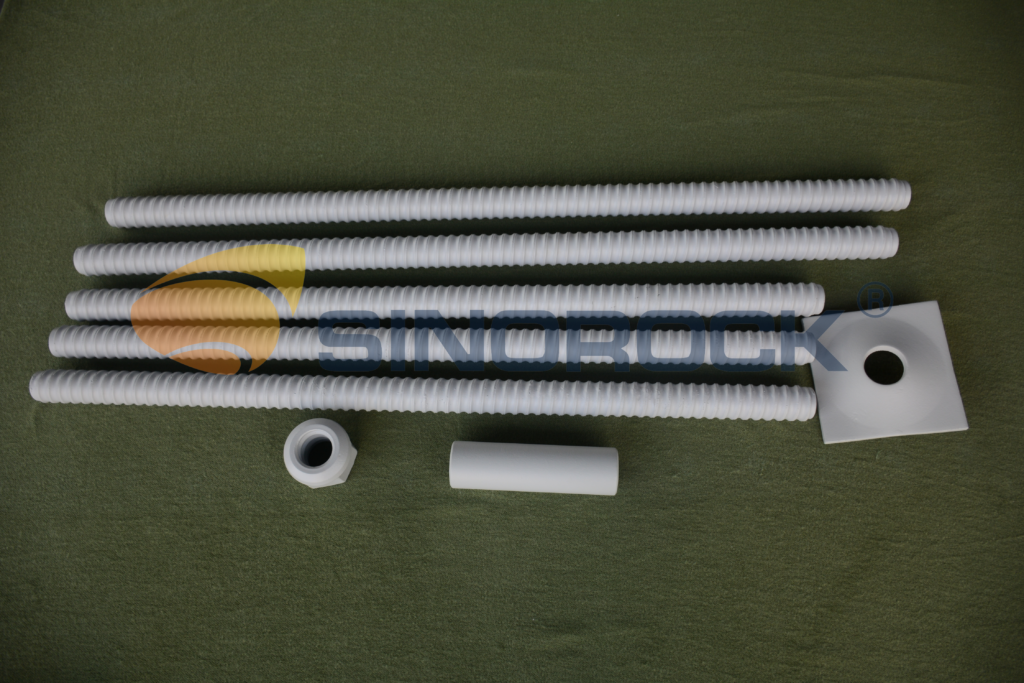
Ordinary self-drilling rock bolts are typically made of steel, which is susceptible to corrosion when exposed to moisture and other corrosive elements present in the rock formations. Corrosion occurs when steel reacts with oxygen and water, leading to the formation of rust. As rust accumulates, it weakens the structural integrity of the rock bolt, making it more prone to failure. This corrosion process not only compromises the safety of the structure but also increases maintenance costs as bolts need to be replaced more frequently.
Anti-corrosion principle of the double corrosion protection self-drilling rock bolt
The double corrosion protection self-drilling rock bolt, on the other hand, addresses these concerns by incorporating advanced corrosion-resistant materials and coatings. These self-drilling rock bolts have a double anti-corrosion process, combining galvanization and epoxy. The process of galvanization is to make the rust-removed anchor bar and accessories immersed in liquid zinc for a certain period of time so that the atoms between them penetrate and diffuse each other, thus forming a layer of iron-zinc alloy, which is dense, uniform, firmly bonded, bright, and corrosion resistant. The insoluble chemicals produced by the interaction between zinc and the concrete solution will prevent further corrosion of the anchor matrix. In addition to the hot-dip galvanized layer, then epoxy powder is sprayed on the rock bolt’s surface again. This process uses an electrostatic spraying method to sprinkle epoxy resin powder on the surface of the anchor rod body and accessories to form an anti-corrosion coating. The coating resists the penetration of oxygen ions, chloride ions, and water molecules, and the strong binding force between the coating and the anchor rod, so the coated anchor rod in concrete has a good anti-corrosion effect. These specialized protective layers act as a barrier against corrosive agents, preventing them from reaching the underlying metal surface.
The Advantages of Double Corrosion Protection Self-Drilling Rock Bolts in Engineering Construction
The advantages of using double corrosion protection self-drilling rock bolts in engineering construction are numerous. Firstly, their enhanced corrosion resistance ensures a longer lifespan compared to ordinary self-drilling rock bolts. This translates into reduced maintenance costs and less frequent replacements, saving both time and money for construction projects. Moreover, the increased durability of these rock bolts enhances the overall safety of the structure, minimizing the risk of sudden failures or collapses.
Another advantage of double corrosion protection self-drilling rock bolts is their versatility in various environmental conditions. They can withstand exposure to high levels of moisture, saltwater, chemicals, and other corrosive substances commonly found in rock formations. This makes them suitable for a wide range of applications, from tunnels and mines to dams and retaining walls. By using these DCP self-drilling rock bolts, engineers can have peace of mind knowing that their structures are well-protected against the harmful effects of corrosion.
Furthermore, the installation process of double corrosion protection self-drilling rock bolts is similar to that of ordinary rock bolts, making it easy to integrate them into existing construction practices. With their self-drilling capabilities, these bolts can be quickly and efficiently installed, saving time and labor costs. Additionally, their corrosion-resistant properties remain intact even after installation, providing long-term protection to the structure.
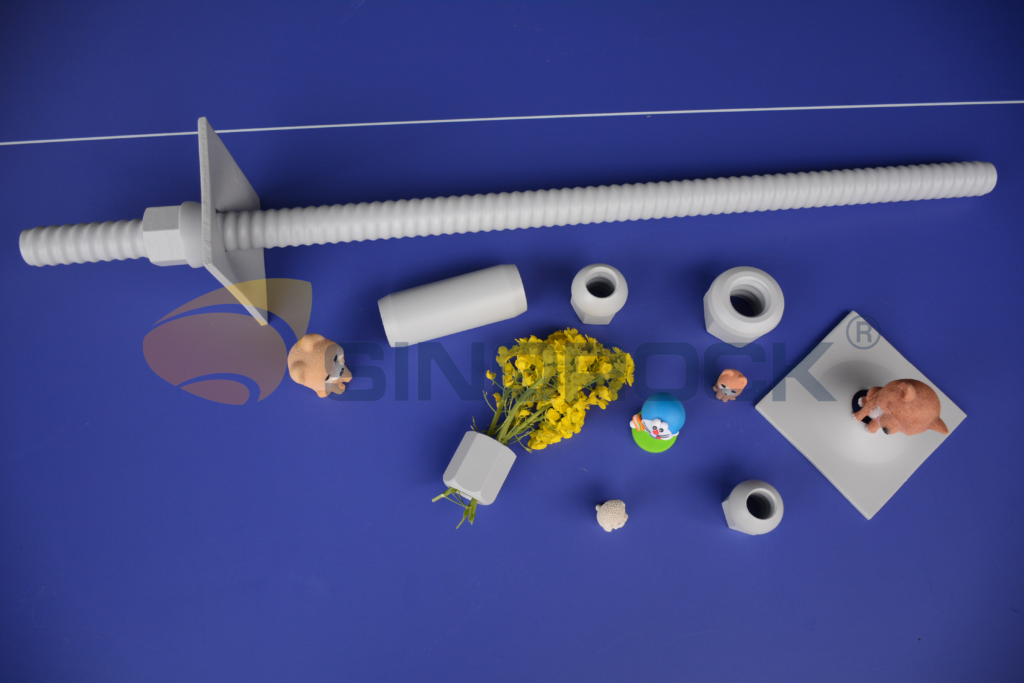
In conclusion, the advantages of using double corrosion protection self-drilling rock bolts in engineering construction are significant. By addressing the harmful effects of corrosion, these DCP self-drilling rock bolts offer increased durability, reduced maintenance costs, enhanced safety, and improved versatility. As construction projects continue to face the challenges of corrosion in rock formations, the adoption of double corrosion protection self-drilling rock bolts will become an essential consideration for engineers looking to ensure the longevity and stability of their structures.